
gvsets_lightweighting_process_final.docx | |
File Size: | 1383 kb |
File Type: | docx |
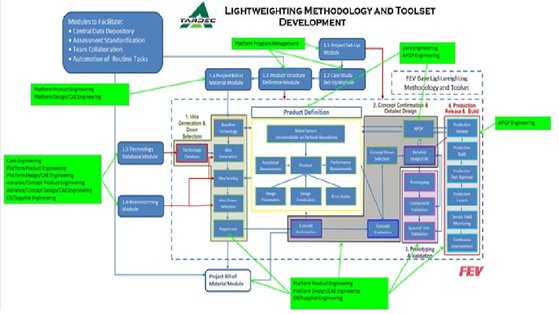
Ground Vehicle Systems Engineering and Technology Symposium
Systems Engineering
August 4, 2016 – Novi, Michigan
Automotive Lightweighting Methodology Adapted and Applied to
Ground Combat & Tactical Vehicle Systems
Greg Kolwich
Charles Schecter
Donald Tirwomwe
FEV North America Inc.
Auburn Hills, MI
Jerry Lane
Great Lakes Systems and Technology, LLC
Chesterfield Twp, MI
Richard Gerth, Ph.D.
Don Ostberg
U.S. Army TARDEC
Warren, MI
ABSTRACT
This paper will discuss how proven automotive systems engineering lightweighting principles and practices are being adapted and applied to combat and tactical ground vehicle systems. An automotive lightweighting methodology has most recently been utilized to reduce the weight of a light-duty pickup truck by 511 kilograms resulting in a 20.8% vehicle mass reduction. A holistic approach to light-weighting offers great benefits with additional mass reduction at a cost savings, reducing the overall vehicle lightweighting cost impact. Automotive studies have shown additional vehicle mass-reductions in the range of 3-5% are achievable when vehicles are aggressively light-weighted (i.e., approximate 20% vehicle mass reduction range). Although many factors like customer usage, function and performance requirements, production volumes, product life cycles, value stream, manufacturing infrastructure, litigation application, etc., are indeed considerably different between automotive and military, these differences do not significantly alter the fundamentals of a robust systems engineering approach to lightweighting.
INTRODUCTIONVehicle lightweighting is a priority for the US. Army. The future force must be more expeditionary and agile to the ever changing global threat environment (Polsen, et al., 2014). Due to increased survivability requirements, additional protection measures have been added to vehicles, which has typically increased their weight. The increased weight has resulted in decreased fuel economy, decreased reliability and associated vehicle availability, and in some cases, decreased swim, fording, and transport capability.
Lightweighting a military vehicle is very complex to execute efficiently with a multitude of factors, requirements and variations to address (e.g. kinetic and blast threat survivability, high mobility in variety of terrains, and extreme thermal environments). Efficiently executing on lightweighting requires a robust systems engineering approach and supporting software tools to facilitate team collaboration, data collection and storage, optimization analysis, decision making and documentation. A proven and flexible lightweighting process, originally developed for automotive applications, has been adapted to advance the state of the art for lightweighting of military vehicles.
An initial impulse may be to assume military and commercial automotive vehicles are too different to be amenable to a common Lightweighting process. Many factors like usage environment, function and performance requirements, production volumes, product life cycles, value stream, manufacturing infrastructure, litigation application, etc., are indeed significantly different. However these differences do not alter the fundamentals of a robust systems engineering methodology.
While the details of the vehicles and associated requirements are different, the type of data and analyses tools used to make engineering decisions are not. Both industries have requirements that flow down to the system, subsystem, and ultimately the component that determine the weight and performance. Both are assembled systems with interfaces across various physical domains that must be taken into account. Both industries rigorously evaluate their systems prior to releasing to the user.
In adopting the automotive systems engineering approach to lightweighting, additional data requirements, tools and processes are introduced. The tools are introduced to ensure consistency, completeness, and design support in the Product and Production Development Phases. The automotive industry generally refers to the tools and processes as APQP (Advanced Product Quality Planning) elements. The APQP tools and processes drive a systems engineering approach to ensure Product and Production Development is lean, timely and efficient. It also ensures product launch in the market place is robust and reliable. APQP is synonymous in meaning to the expression “measure twice, cut once”. Because the APQP system is a systems engineering approach, it has many similarities at the higher levels with the DOD 5000.02.
LIGHTWEIGHT METHODOLOGY AND TOOLSETThe lightweighting methodology, which is integrated into a product development process, is founded on systems engineer fundamentals. The systems engineering process is a top-down, comprehensive, iterative and recursive problem solving process, applied sequentially through all stages of development (Department of Defense, 2001). It is used to:
· Transform needs and requirements into a set of system product and process descriptions (adding value and more detail with each level of development),
· Generate information for decision makers, and
· Provide input for the next level of development
Figure 1. Lightweighting Methodology Overview
The lightweighting methodology is constructed of four primary phases (see Figure 2): 1. Idea generation and Down selection, 2. Concept Confirmation and Detailed Design, 3. Prototyping and Validation, and 4. Production Release and Build. Within each phase, key tasks are supported with industry proven processes and tools (see Figure 1). The process is very modular promoting a check and balance approach during and at the completion of each major phase. The modular approach also facilitates a diversified team approach enabling multiple organizations to work on smaller, individual tasks and deliverables. These deliverables create the discrete building blocks for the completion of the major task or phase and provide the input for the next level of development.
Figure 2: Automotive Lightweighting Approach
PHASE 1: IDEA GENERATION AND DOWN SELECTIONThe starting point for any product optimization process, including lightweighting, is understanding the functional and performance requirements of the product and interfaces under analysis. This highlights another major difference with military programs versus commercial industry. In military programs, the government states relatively high level vehicle and subsystem requirements, and the vehicle manufacturers translate those requirements to specific component loading conditions based on their particular vehicle design. Since the government does not own the TDPs or the component design rational, it does not know the specific component requirements. This makes determining the applicability of specific lightweighting technology challenging.
Next is to identify the boundary conditions and constraints within which the team must conduct the optimization process [e.g. technology readiness level (TRL), manufacturing readiness level (MRL), cost, timeframe, etc.]. Establishing an analysis “rulebook” of boundary conditions and constraints is paramount to ensuring the team as a whole meets the higher level project objectives. Lightweighting ideas are generated through a variety of means, such as supplier investigations, technology databases, subject matter expert brainstorming, etc. A process of idea scoring and down-selection, based on the analysis boundary conditions and constraints, helps reduce the compilation of lightweighting ideas to an optimized solution for final report out. The report out becomes the input for Phase 2, the next level of evaluation and down-selection to a final solution. The key tasks of Phase 1 are highlighted in Figure 3.
Figure 3. Lightweighting Phase 1 Subtasks.
Baseline Technology EvaluationThe Baseline Technology Evaluation is a process of taking the concept or productionized product and logging it into the applicable product structure template as agreed by the team. Data is organized by application and standardized product structures to support efficient entry and retrieval of data for current and future projects. Included in the baseline evaluation and setup is connectivity to all supporting functional and performance requirements/specifications, guidelines, product attribute data, and all other supporting product definition documentation, such as key APQP documents (e.g. Boundary Diagrams, Interface Diagrams, DFMEAs, etc.). Baseline data is stored at all levels of the product structure (i.e., vehicle, system, subsystem, sub-subsystem and assembly/component).
The baseline data will not necessarily be complete for the intended analysis purposes. Further, it does not have to go to equal Work Breakdown Structure (WBS) depth across the vehicle. The depth must be sufficient within the sub-system to conduct the lightweighting analysis, which will be driven by the type of technologies being considered. For example, if a lighter weight engine is being considered, then the engine power plant may be the lowest WBS level. However, if specific technologies within the engine, such as a lighter weight engine block is being considered, a lower level WBS may be necessary. Hence, there is an interaction between this step and the other steps, and a continuous baseline data collection effort should be planned for.
Idea GenerationConnected to the project boundary conditions, a lightweighting BOM is created from the baseline BOM to initiate the idea generation process. Idea generation can happen at any WBS level (system, subsystem, sub-subsystem, assembly/component). The Technology Database, the warehouse for lightweighting ideas and concepts, provides the team with relevant lightweighting data. During a project, new ideas are entered in the database. Various sources of data including benchmark data, previous published literature, material and manufacturing supply base, prior completed studies, academia, subject matter experts, etc. are used to populate the Technology Database.
The objective of the Technology Database is to extract and centrally locate data from “shoeboxes” and “silos” to a central depository promoting team brainstorming and collaboration. The database has various categories (e.g., material, manufacturing, technology substitution) which provide different pathways to search for lightweighting ideas. Ideas are later screened by a review team that considers the rulebook to determine applicability, feasibility, and database compliance of the various ideas.
Idea ScoringThe ideas and concepts the review team deemed applicable and feasible according to the rulebook are compiled into a Down Selection Matrix (DSM). Ideas are organized and grouped by product structure. For each idea logged into the DSM, supporting facts of the lightweighting concept are captured. Each idea is then scored against weighted factors. The down-selection factors and applicable weighting are assigned upfront in the analysis during agreement of the case study boundary conditions and constraints (rulebook).
At this time there are usually too many ideas and insufficient information on many of them to move forward with concrete optimization recommendations. An initial idea scoring threshold is established based on project schedule, available resources, degree of information required for the various ideas, and other project related constraints established in the rulebook. Ideas that meet the initial scoring threshold, are evaluated further by gathering additional supporting data. More precise calculations on mass reduction and cost implications are completed in Brainstorming Calculator Worksheets. This information is entered back into the DSM providing additional scoring intelligence.
Idea Down SelectionUsing the preliminary mass and cost calculation data, along with key scoring metrics such as TRL and MRL and any other metrics from the rulebook, a final down-selection is made on those ideas to move forward on. Depending on the project scope there could be hundreds of ideas that meet the acceptance criteria. In addition many of the ideas can be defined as standalone ideas or grouped with other ideas to create combination solutions. This is true at all WBS levels: combining ideas to make various component/assembly solutions, combining component/assembly solutions to make sub-subsystem solutions, combining various sub-subsystem solutions into subsystem solutions and so on. The process of bundling and rolling-up lightweighting ideas into higher WBS levels is the foundation of the optimization process. The team then reviews and selects bundled lightweighting subsystem concepts forming system solutions and a potential vehicle solution. In many cases, multiple vehicle solutions are selected to pursue in the Phase 2 analysis.
One or several of these vehicle solutions are selected along with the evaluation of potential secondary mass savings (also known as mass compounding). Secondary mass savings are the additional lightweighting benefits offered through a holistic vehicle lightweighting approach. As the vehicle becomes lighter, it may be possible to “downsize” select systems (engine, transmission, suspension, fuel, exhaust, etc.) to accommodate the lighter loads without sacrificing function and/or performance. The compounding benefits can yield 15-30% additional system weight reduction (3-5% vehicle weight reduction) at 100% cost savings.
Report OutDuring the Report Out process the team prepares their recommendations for the Concepting and Confirmation Phase (Phase 2). This includes a summary of the lightweight initiatives from the component level up through the final vehicle solution. Key metrics are presented highlighting mass, cost, TRL, MRL and other business case assumptions. The Report Out process takes place in two steps. In the first step, the core team (team responsible for developing the Phase 1 final vehicle solutions) reviews and assembles a recommended prioritization schedule for the Phase 2 effort. In the second step the core team presents the results and recommendations to both the end customer and the team members responsible for conducting the Phase 2 tasks.
PHASE 2: CONCEPT CONFIRMATION AND DETAILED DESIGNThe Phase 2 effort begins with Concept Optimization; components are modeled and optimized to the provided specifications at all applicable product structure levels (e.g. assembly, system, vehicle). The initial focus is solely optimal mass reduction, with no impact to function and performance. As preliminary solutions are taking shape, members of the support team (e.g. manufacturing, cost, quality, supply-chain, procurement, serviceability, etc.), are evaluating the concepts, providing input to the design team, supporting a more comprehensive attribute optimization process. Ultimately design alternatives, based on weighted attributes, are ranked in a Pugh Matrix. A final down-selection is made in which a production intent design is selected. As the design transitions from the concept phase, to a production intent phase, Advanced Product Quality Planning initiatives are accelerated to ensure a robust and reliable product is developed. The key tasks of Phase 2 are highlighted in Figure 4.
Figure 4. Lightweighting Phase 2 Subtasks
Concept Optimization During Concept Optimization the design team further develops the concepts proposed in Phase 1. The primary objective is to minimize weight while maintaining function and performance. The process starts with a review of current specifications to determine if new performance evaluation criteria are required to address lightweighted component material and manufacturing changes. This task is initiated through Advanced Product Quality Planning initiatives. Adjustments are made to analysis boundary conditions and recorded in the engineering specification. The same evaluation takes place at all WBS levels (i.e., component, assembly, subsystem, system, vehicle). Simultaneously, engineers are reviewing and acquiring necessary material and joining properties to support the CAE analysis. In the absence of validated material and joint models, the team works with industry experts to approximate the anticipated mechanical properties until lab testing can be conducted. In the military environment, blast and ballistic data for novel materials are often not available and require coupon level evaluations to obtain.
Often the optimization process begins before all model inputs have been finalized. Rather the process begins with the available information and continues to expand as new information becomes available. A combination of CAD, CAE and optimization software tools are used in the optimization assessment. The level of automation, and sequence, is generally driven by part and/or system complexity and modeler experience. In many cases several part derivatives, as reported out in Phase 1, are under evaluation to determine a final lightweighted solution.
For existing vehicles, the aforementioned requirements become very important here. The analysis cases and their boundary conditions can often be derived from the vehicle and subsystem level requirements. However for anyone other than the original equipment manufacturer (OEM), the magnitude of specific engineering loads that the subsystem experiences are often assumed and degree the loads propagate through the system are often unknown. Reverse engineering to determine components’ loading requirements often assume the components’ capabilities are the requirement. Under that assumption, the components are generally optimized within their material and further weight reduction through topology optimization is unlikely. TARDEC is examining processes to overcome this limitation.
As the optimization process progresses, engineering support from other disciplines (e.g. manufacturing, cost, quality) increases to ensure parts are robust, manufacturable, and fall within the defined costs targets.
Concept EvaluationDuring Concept Evaluation, the team compiles all analysis data to complete the final evaluation. This includes how each design compares to the defined function and performance requirements. Other evaluation parameters, as defined up-front in Phase 1, are also compiled. The evaluation parameters include, but are not limited to:
· Technology Readiness Level (TRL)
· Manufacturability and Mfg. Readiness Level (MRL)
· Serviceability and Repairability
· Prototype cost and timing estimates
· Production cost and timing estimates
· Special capital investment requirements
· Supply chain road map (identification of Government Furnished Equipment, MIL DTL and MIL STD requirements for new materials, depot considerations, potential material suppliers, distributors, manufacturers, etc.)
For each parameter considered, a rating scale is established to grade concepts relative to one another. A common scale (i.e., 0 to 100) is used for all parameters, regardless of their importance in the overall decision process. The rating scale is based on several factors/attributes, each factoring into an overall score/grade. For example grading the parameter Serviceability, is based on factors such as time to service, ease of serviceability in the field, cost of service, special equipment/tools required for service, etc. Prior to the initiation of the Concept Down-Selection step, an evaluation worksheet, for each parameter, is completed with all ideas graded.
Concept Down-Selection The Concept Down-Selection process is similar to an Analysis of Alternatives (AoA). A Pugh matrix is assembled to tabulate and objectively assess all the evaluation parameters considered in the analysis. The rows of the Pugh matrix represent the evaluation parameters. Each column references a concept and the associated scoring for each corresponding parameter. Parameter importance, with respect to other parameters, is addressed through a parameter weighting factor. Concept scores are multiplied by parameter weighting factors to arrive at net scores for each parameter and each concept. Parameter importance weighting factors, carried over from the Phase 1 analysis, are initially referenced. Based on the data acquired in the Concept Evaluation stage, the team collectively reviews the weighting factors and decides if adjustments are required to drive resolution and separation between the competing concepts. A final score is tabulated for each concept; the concept with the highest score moving forward as the production intent design.
Production Intent DesignNow that a production intent design is selected, all product and production development tasks are centered on a single design. The initiation of Advanced Product Quality Planning (APQP) tools and processes is the starting point to ensure the production intent design meets all requirements, at all product structure levels (i.e., component, assembly, subsystem, system, vehicle), and is robust, reliable and cost effective (additional details below). All applicable guidelines and specifications are compiled into a Design Verification Plan and Report (DVP&R) to ensure all requirements are being tracked and met during the product development process. All guidelines and specifications including Function, Performance, Safety, NVH, Manufacturing, Material Restrictions, Serviceability, Shipping and Handling, etc., are included in the DVP&R. When new requirements or missing specifications are discovered during the APQP processes, updates are made and tracked in all relevant documents including the DVP&R.
As the production intent designs are refined, preferred prototype and production sources are solicited for manufacturing and cost optimization input. Supply base input is utilized during the 3D CAD development stages through to the finalization of 2D drawings. Keeping the cross functional team (e.g. design, manufacturing, quality cost, procurement, supply chain) engaged during all stages of product development and productionization helps ensure the end product meets all objectives within the defined boundary conditions.
Advanced Product Quality PlanningIn Phase 1, APQP documents are referenced to support the initial Idea Generation and Down-Selection activities. Key documents are referenced to gain an understanding how components function and interface with neighboring components/systems, what performance criteria exist, what error states occur when function and/or performance criteria are not met, and what virtual or actual tests are conducted to verify and validate designs.
For modified designs or new designs with similar function and performance requirements, surrogate product APQP documents are used as the starting point for the next generation designs. For all-new production designs and applications, less applicable documentation and product history may exist requiring new clean sheet documentation as the starting point.
As the product transitions from concept to a production intent design, product specific APQP initiatives are started. Key documentation such as Boundary and Interface Diagrams, Parameter Diagrams, DVP&Rs, DFMEAs, PFMEAs, Control Plans, etc. are customized to the product under development. As new functional and performance criteria are uncovered, design and test specifications are updated to ensure future design derivatives are adequately designed and developed.
This is particularly important for lightweighting technologies, since material substitution and multi-material joining plays a significant role in reducing vehicle mass. For example noise factors such as temperature, humidity, chemical, shock loading, etc., may be benign to existing, heavier, ferrous structures and thus never captured in test specifications for validation. Omitting these noise factors for polymer based designs could be catastrophic. This example is a simple one-dimensional problem. Unfortunately as technology advances, the problems are not simple and one dimensional. Without sufficient APQP tools and processes in place, the odds of field failure and higher severity failures, grows exponentially.
PHASE 3: PROTOTYPING AND VALIDATIONIn Phase 3, components, systems and vehicles are built and tested to ensure physical hardware performs as predicted by CAE simulations. The checks and correlations are not only made for functional and performance attributes, but also for part fabrication, assembly, serviceability, etc. Correlation between physical test/analysis and CAE simulation results are used to tune virtual models to support further optimization. In the lightweighting realm, this correlation and characterization step is extremely important for advanced materials with little or no history for both the current project under evaluation and any future projects. The key tasks of Phase 3 are highlighted in Figure 5.
Figure 5. Lightweighting Phase 3 Subtasks.
Prototyping Prototyping, when done right, accomplishes two major objectives: (1) verifies integrity of the theoretical calculations, and (2) supports analyses where theoretical evaluations lack the requisite reliability and confidence and/or where physical parts provide a more accurate assessment of the situation (which may be based on current toolset status within industry).
In the first instance, advanced simulation tools have exponentially increased the amount of theoretical analysis work that can be performed early in the product development process. Verification through simulation significantly reduces the number of problems experienced during prototype builds and/or minimizes the size and cost of the builds. This is true not only from a functional and performance verification perspective (component through to vehicle level), but also includes manufacturing (e.g., primary fabrication, material joining and assembly, factory floor human ergonomics) and serviceability simulations (e.g., tools, ergonomics, repair time).
In many cases unfinished production tools can be produced to support prototype builds eliminating the costs of expensive prototype tools. For new advanced technologies, including lightweighting, a period of learning is required to gain confidence between the simulation and physical test results. However, this confidence may be short-lived as new technologies are under continuous development. Under a robust systems engineering approach, the model correlation, tuning and capturing of lessons learned via guidelines and specifications ensure future models are more reliable than their predecessors. This will ultimately lead to more efficient and effective use of prototypes helping reduce costs and improve product and production development timing.
Component VerificationUnder a robust system’s engineering methodology, testing requirements are a direct output of a robust APQP process. The Parameter Diagram, defining error/failure states to function and performance, the DFMEA, identifying failure severity, potential causes of failure, and current detection design controls, all culminate with the development of comprehensive specifications. In many cases surrogate component design and test specifications exist which may cover a good portion of the required test requirements for next generation products. Through the APQP process, new requirements and specifications, unique to the design and/or application, are developed and integrated into a new set of specifications. Component testing new technologies, like lightweighting, to existing specifications will likely result in premature field failures.
Once new test requirements are identified, component test specifications are developed with the ultimate goal of reproducing real world customer usage in a laboratory environment. Other important considerations (including trade-offs to vehicle level testing) include test repeatability and reliability, data acquisition (pre, in-process, and post), equipment complexity and cost, sample size, and test duration.
Figure 6. Cascading of Knowledge and Work Effort Through the Product Structure.
Finding the right balance of component laboratory testing versus vehicle level testing can be challenging. The goal should always include heavy upfront component verification and validation, with a reduction of testing at the vehicle level when possible. This helps reduce project test cost and promotes successful vehicle level testing by minimizing project delays due to vehicle test failures.
System / Vehicle VerificationSimilar to component verification and validation, vehicle level testing requirements and specification are also driven through the standard APQP processes. Although great inroads have been made on improving CAE simulation software aimed at evaluating component, subsystem and system interactions, it is by no means a paint-by-numbers operation. From unique component interfaces, exponential usage of non-isotropic materials, multi-material joining technologies, manufacturing processing variation considerations and unique customer usage profiles, the problem is quite complex at the vehicle level. Add in the rapid advancement of new technology, with limited prior modeling knowledge, and one may wonder how anyone could ever be successful. Physical vehicle testing, if performed right, provides the confidence that these complex and layered interfaces and interactions are contained within the requirements of the vehicle. There will always be a need for vehicle level testing. The question is how we maximize its benefit while minimizing its cost (i.e., fewer vehicle builds, shorter test durations, more pinpointed testing, etc.). The simple answer involves adopting a systems engineering approach (evaluate, learn, iterate, store, cascade, repeat); a top-down, bottoms-up approach as shown in Figure 6. This is analogous to the DOD Systems Engineering V-structure.
PHASE 4: PRODUCTION RELEASE AND BUILD The fourth and final phase is the Production Release and Build Phase. Although this is the final phase, production considerations are initiated up-front in Phase 1 as part of the initial Idea Generation and Down-Selection task. In Phase 2, additional manufacturing and production considerations are included in the final production intent design selection. From this point forward production planning and manufacturing APQP activities increase at an exponential rate in preparation for production builds. Early cross functional team deployment (product, manufacturing, quality, cost, supply chain, etc.) is the best chance for a successful on-time launch. This is especially true with new advanced technologies, where minimal production experience may exist.
Key upfront production tasks include the Production Release, Pre-Production Builds, Product Part Approval Process and Production Launch. Post production launch activities often center on Service Field Monitoring and Continuous Improvement. These tasks are broken down into numerous subtasks and involve participation from many of the cross functional team members. The key tasks of Phase 4 are highlighted in Figure 7.
Figure 7. Lightweighting Phase 4 Subtasks.
Production Release The Production Release starts as Phase 3 prototyping and testing tasks are winding down. Upon successful completion of the DVP&R and other key APQP documents, the team has the confidence to kick-off production tooling and equipment. Engineering drawing and specification documents are reviewed and signed-off by product, manufacturing and quality team members. Manufacturing tooling and equipment specifications are reviewed and signed-off between corporate manufacturing and the assigned production facility. Drawings and quote packages are sent out to the supply base by the procurement specialist group. The PM along with cost engineering tracks key metrics (cost, mass, timing) and overall production launch readiness to ensure all project deliverables are being maintained.
Production BuildProduction Builds start immediately as first-off parts are delivered from production tools and part suppliers. The goal is to validate fit, form and function as quickly as possible to ensure components are ready for the Production Part Approval Process (PPAP) line run-offs. First-off parts are also used to support tooling and fixturing run-off and qualification, and measurement system qualification. Part run-offs transition from tools shops to the production facilities where final installation and debugging takes place. APQP support documents are updated (PFMEAs, Control Plans, Work Instructions, SPC Charts, Rework Procedures, etc.) with any final changes made to production parts and/or equipment.
Production Part ApprovalThe Production Part Approval Process (PPAP) starts at the component level and builds-up to the final vehicle level. PPAP requirements and standards are published by various industry action groups (i.e., like the Automotive Industry Action Group) to ensure proper tasks are carried out, and supporting documentation is in place, facilitating the successful release of the product to the end customer. The PPAP process and documentation can be thought of the final collection of APQP records and documents at the time of production launch.
Production LaunchOnce all parts have successfully completed PPAP, a Part Submission Warrant (PSW) approval is given indicating parts can be shipped to the end customer. Saleable end customer vehicles can only be built with PSW’ed assemblies, and PSW’ed assemblies can only be built with PSW’ed components. This build control ensures full traceability throughout the entire vehicle product structure.
Although the goal is to achieve 100% first time quality during product launch, issues will arise. Part defects, handling damage, manufacturing takt time issues, delivery issues, sequencing issues, etc., are all very plausible during complex vehicle builds. Having a robust quality action plan to quickly assess and resolve these issues is very important. Equally important is tracking this information back into applicable APQP documents to ensure the lessons are captured for the next generation product.
Service Field MonitoringAs new technologies are manufactured and released into service, systems are required to monitor product health with respect to service hours. At all product structure levels, estimated field failures as a function of production parts in the field and timeframe should be established upfront as part of the APQP activities during Phase 2. Tracking service repairs relative to time in the field targets can highlight potential escalating problems. Design and manufacturing changes can be made to minimize the suspect product in the field.
Regardless of how big or small field service/repairs are on a given product, this information is very valuable. It helps confirm disconnects between assumptions captured in key APQP documents (P-Diagrams, DFMEAs, Specifications, etc.) and real world findings. Transferring this learned information back into the system helps ensure problems are resolved and not carried forward into future designs or other applications.
Continuous ImprovementContinuous improvement can be categorized as reactive or proactive. Driving continuous improvement as a result of service field monitoring would be considered reactive improvement. Increasing performance, reducing weight, and reducing costs are examples of proactive continuous improvement. For new advanced technologies continuous improvement is a double edge sword. On the one side, because the technology is new and likely still evolving, the lure of adopting the next best derivative is very appealing. On the other side, because the technology is new, field experience may be limited making continuous “improvement” very risky.
Ultimately risk versus reward drives the level of continuous improvement implemented. Taking a systems engineering approach, adopting the latest and greatest engineering tools, and following a robust APQP process all promote safe continuous improvement implementation.
Conclusion and SummarySo why should we consider lightweighting military vehicles? Currently it appears the benefits of lightweighting on an individual attribute basis doesn’t outweigh the risk and/or potential cost implication of lightweighting. That is, the benefit of lightweighting towards improved mobility, or fuel efficiency, or transportability, or reliability, when considered individually against cost and risk, is rendered unrealizable. This is particularly true, because each attribute is related directly or indirectly to a requirement. Weight is considered the result of a design process where the individual requirements are often treated as independent. This often leads to a weight growth spiral. When the combined impact of the weight growth is considered across all attributes over the entire life-cycle, the value becomes more apparent. .
A complimentary approach to enhance the positive benefits of lightweighting is to work towards eliminating additional direct manufacturing costs and minimize the product and production development risks. Eliminating or minimizing direct manufacturing costs (DMC) for lightweight technologies in the short-term, and perhaps even over the long-term, may be very difficult to achieve. So the notion of implementing a lightweight technology because it costs less is not very realistic. However when the Total Cost of Ownership (TCO) is considered (DMC, Fuel Savings, Transportation, Service and Repair, etc.), the business case of lightweight begins to show value.
To further improve the business case, eliminating or minimizing product and production development risks is key. The last thing any one entity wants, internal or external to the military, is to make a change which puts soldier’s lives in jeopardy. The goal of lightweight should be quite the opposite. In addition with long product life cycles and low production volumes, the approach must be based on targeting 100% upfront success. A Systems Engineering approach to lightweighting, and product and production development as a whole, is truly the only efficient and effective way of minimizing risk and achieving success.
DisclaimerReference herein to any specific commercial company, product, process, or service by trade name, trademark, manufacturer or otherwise, does not necessarily constitute or imply its endorsement, recommendation, or favoring by the United States Government or the Department of the Army (DoA). The opinions of the authors expressed herein do not necessarily state or reflect those of the United States Government or the DoA, and shall not be used for advertising or product endorsement purposes.
References 1. Department of Defense. (2001). Systems Engineering Fundamentals . Fort Belvoir, VA: Defense Acquisition University Press.
2. Polsen, E., Krogsrud, L., Carter, R., Oberle, W., Haines, C., & Littlefield, A. (2014). Lightweight Combat Vehicle Science and Technology Campaign. Warren: US Army Tank Automotive Research, Development, and Engineering Center, Report # 25940.
Figure 7